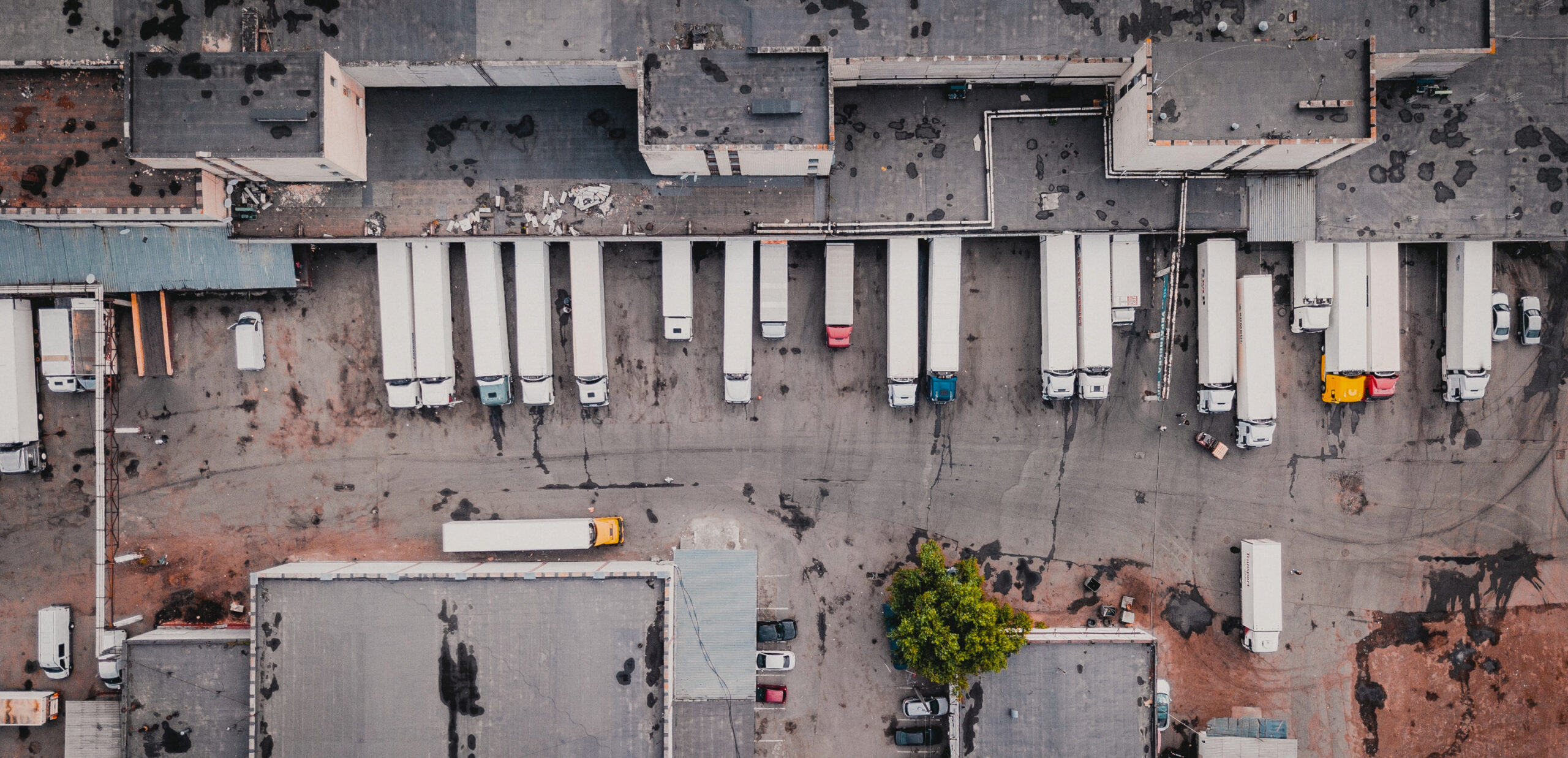
How It Works
How it works
Where is the product we ordered? When will it get here? Why does it take so long to get from the warehouse to the jobsite? These are some of the questions that keep us up at night and wake us from sleep early in the morning. Real concerns that can make a customer’s day more problematic or take a load off their shoulders. It seems easy enough; an order is placed and the delivery is made. Press the buy button and the stork delivers the nicely wrapped package just as you walk out your front door to grab the morning paper. Right? If only we had a super fleet of storks to make our timely deliveries.
Transportation and logistics, material procurement, customer service, and on location technical guidance is an art that AMICUS works daily to make more efficient and effective for their customers.
Timelines for Delivery
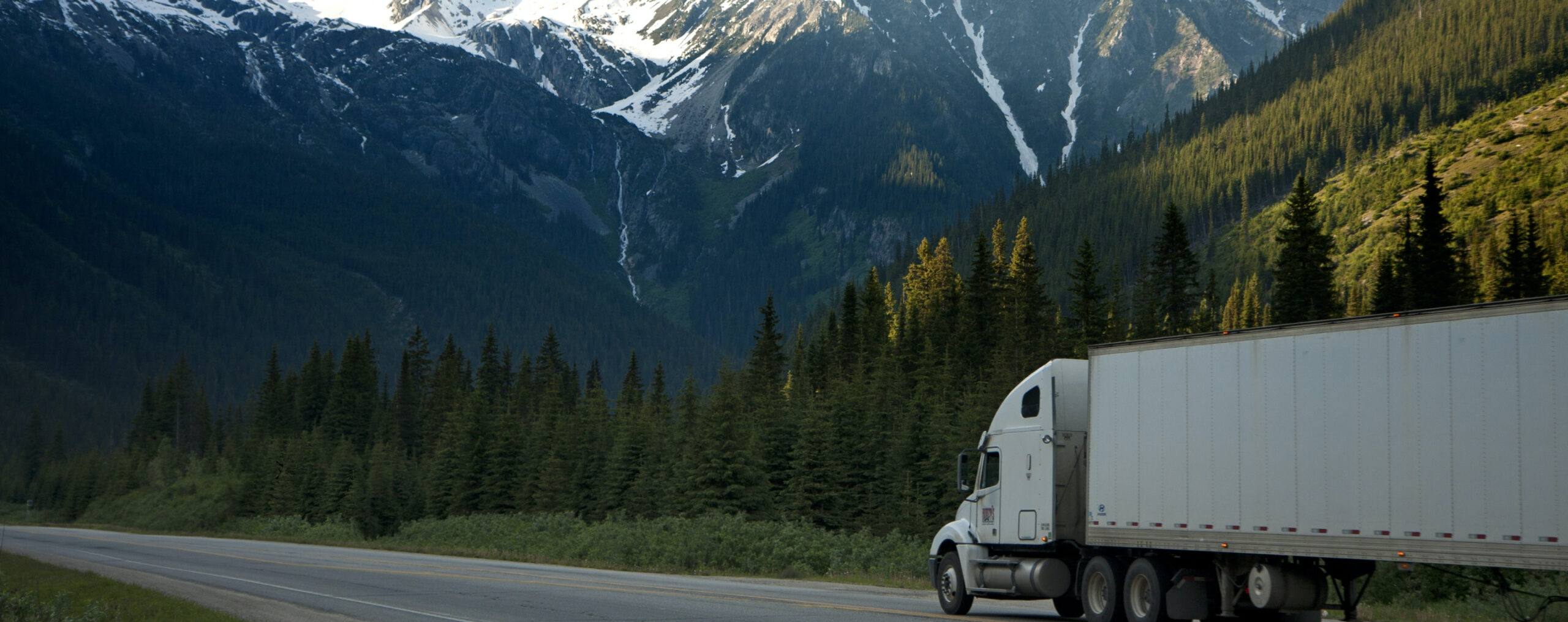
The AMICUS logistics team receives the information that an order is ready to ship. They start contacting carriers in our vast database to see who has a truck near the pick up location that would like to travel to the customers destination. Once a driver is paired with a load they schedule a pick up with the shipping location for a specific date and time. The driver loads the material, sets course to the destination, and heads out on the open road. Drivers can typically travel 500 to 600 miles a day, which means if the total miles of the trip is 2000 miles then they will arrive at the destination in 3.5 to 4.5 days depending on weather and traffic conditions.
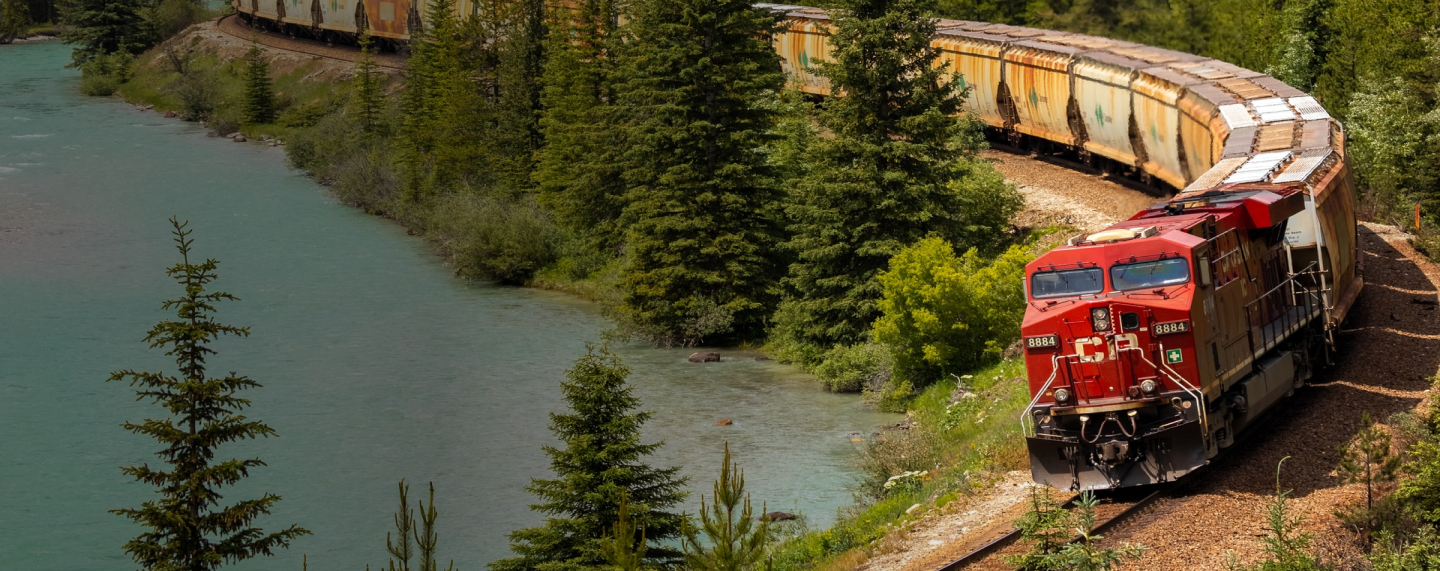
AMICUS operations place an order with the plant, the plant requests a specific railcar type, fills the car and communicates with the railroad the route and destination. The car leaves the plant and operations lets logistics know that the car has shipped. Logistics then tracks the car from the shipping location to the railyard destination. Logistics and operations then work with the transloader and local carrier to schedule deliveries to the customer.
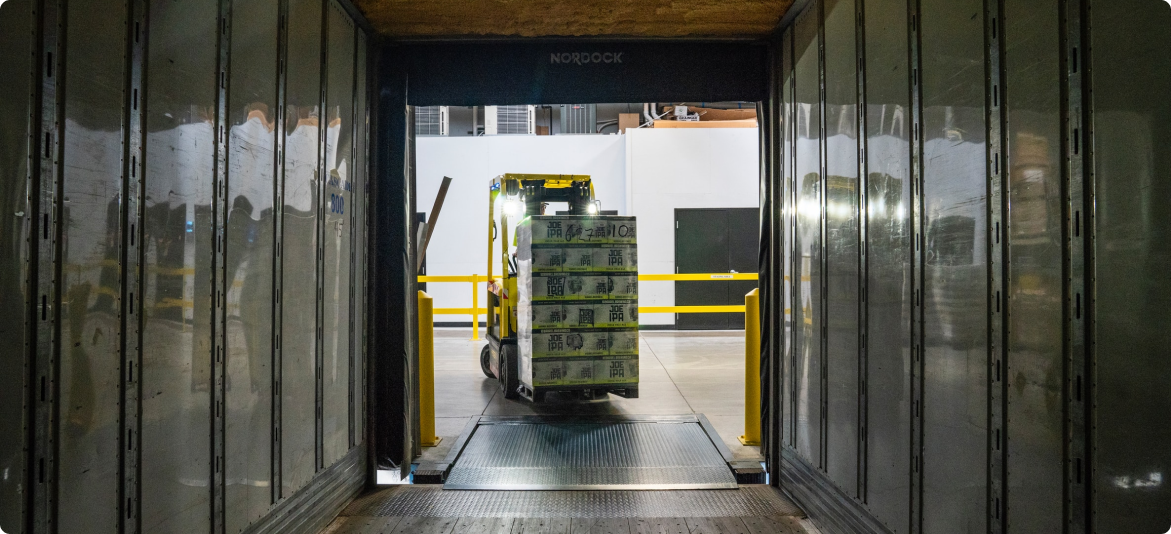
Single or multiple pallets can be shipped by a carrier that specializes in less than truckload (LTL) shipments. Carriers that perform these tasks help shippers who can’t fill a full truckload. Logistics chooses a carrier through an online portal based on price and availability. Prices are based on the dimensions and weight of the pallet(s) being shipped. The carrier is chosen and scheduled to pick up and deliver on the preferred dates. Once the pallet(s) have been picked up, the logistics team tracks the shipment on its journey to the customer.
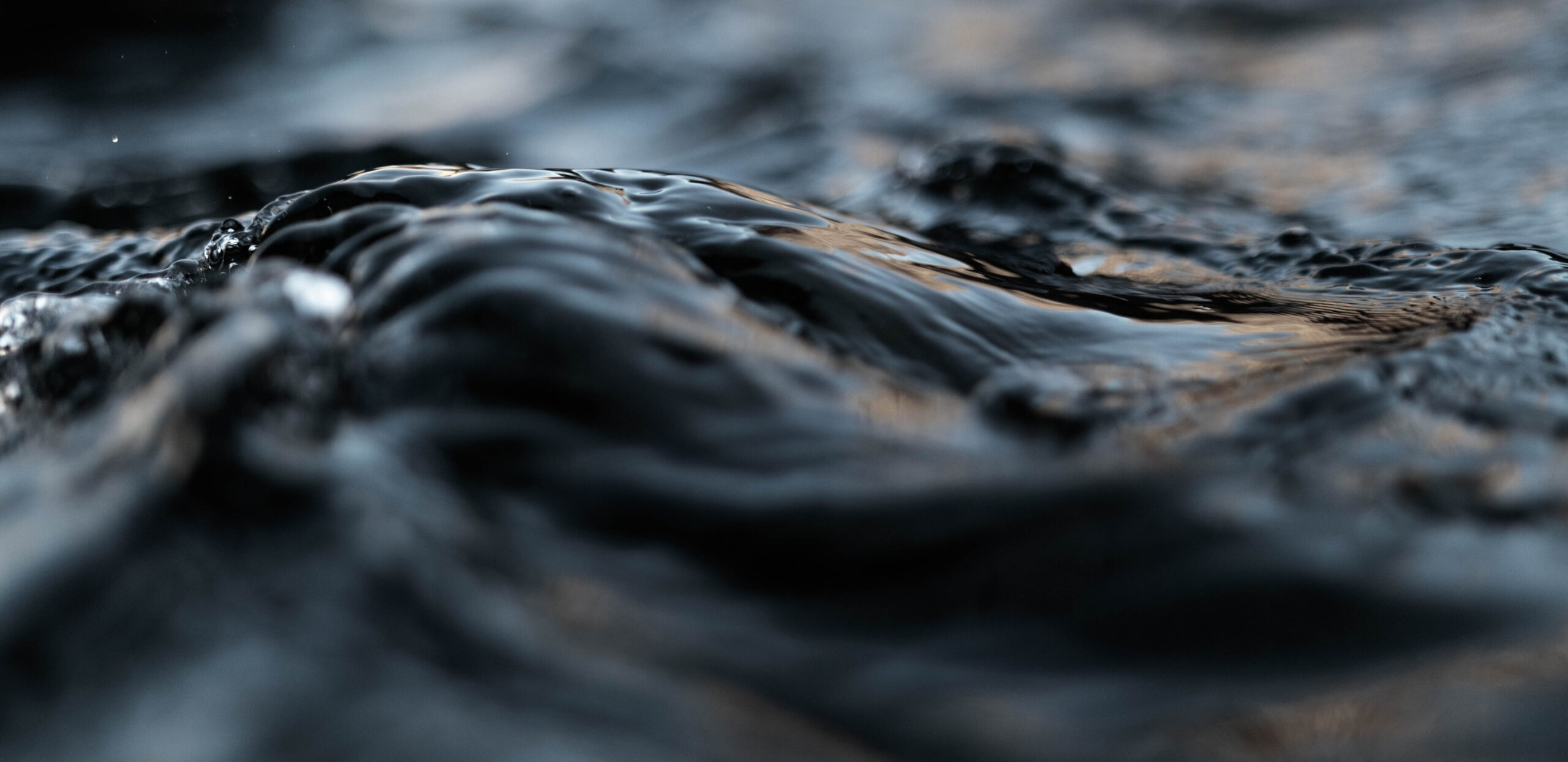
Logistics arrange for a truck to pick up the material from the plant and deliver it to the staging warehouse. The drayage company brings a container to the staging warehouse where it is loaded, inspected, and sealed. The drayage company then brings the container to the port where a gantry crane loads the container onto the sea vessel. The ship takes the container to its destination port where the customer receives the material.
Roadmap for Success
Years of learning from wrong turns, right turns, exploration, victories and defeat have given the AMICUS team the experience to provide quality solutions for its customers. Each project is different in its own unique way, which demands a different roadmap to ensure its success.
It starts with listening to our customers as they give the details of their projects. Not just the materials we can provide them or the ground conditions they will encounter, but all of the challenges they will encounter. The details matter!
After discussions with the client, the AMICUS team creates a number of options that will help the project succeed.
The Journey
What does the customer experience when working with AMICUS?
Thoroughness and dedication to the details of the customer’s needs is of the utmost importance. The customer’s journey with AMICUS begins with the first phone call, email, or handshake. AMICUS will then take the time to learn as much as they can about the project, then:
- Recommendations are sent along with information and pricing for the materials.
- The opportunity to support the project is awarded to AMICUS.
- The AMICUS Operations, Logistics, and Accounting teams meet to discuss the details of the project.
- Operations place the orders with the different manufacturing plants and warehouses.
- Logistics starts working with the railroad, trucking companies and shipping locations to arrange loading dates and times.
- Logistics reaches out to the customer contact at the delivery location to discuss delivery requirements.
- Operations receives release numbers and ready dates from the shipping locations and hands them off to Logistics.
- Logistics makes the final arrangements with each transportation entity to ensure the material is loaded on the required date and time.
- Logistics tracks the train cars and trucks from the shippers locations to the customers project location. Updates are given to the point of contact at the job site during transport and prior to arrival.
- Logistics receives a signed proof of delivery from the transportation entity once the delivery has been completed and then sends it to Accounting.
- Accounting creates an invoice, attaches the proof of delivery and sends it to the customer.
- Throughout the course of the project members of the AMICUS team will check in regularly with the key personnel for the project to see how the job is progressing. If changes are need to be made, AMICUS will adjust the Roadmap to ensure the success of the project.
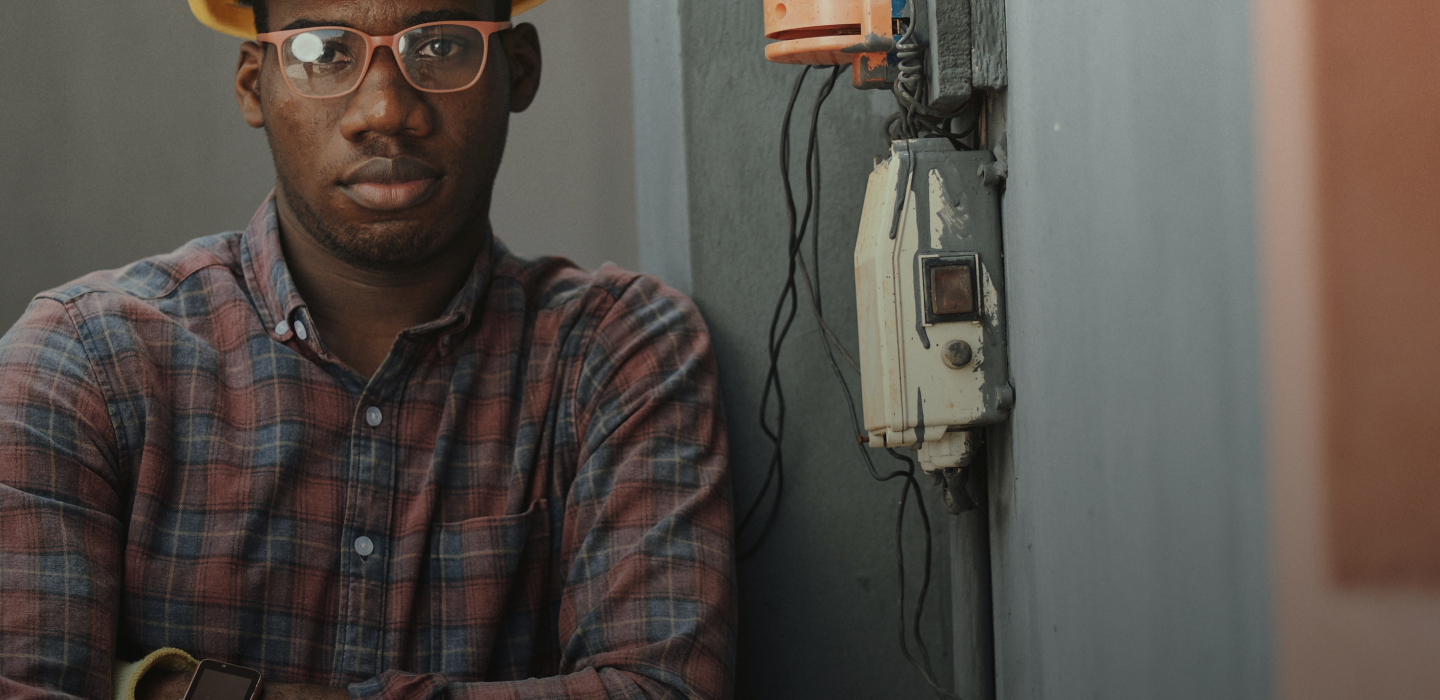